Role of 3D Printing in Product Design and Development
- Karthikeyan Prakash
- Mar 19, 2021
- 2 min read
The product development life cycle follows the journey of an idea from the drawing board to the final finished product. In this blog, I am going to explain the product outer enclosure manufacturing and the use of a 3D printer in the design evaluation stage. There are 4 key stages that every product development goes through,
Ideation Stage
Design Evaluation
Planning Stage
Manufacturing/Producing
Ideation Stage
In this stage, the design and development team discovers new cutting-edge technologies or possibilities in product development. An Animated or sketch board of how the finished product should look helps industrial designers to prepare BOM, dimensions, materials to be used, and test plans. It is also important at this stage to decide on workflow, operations, and supply chain.
Sample Product Design Sketch
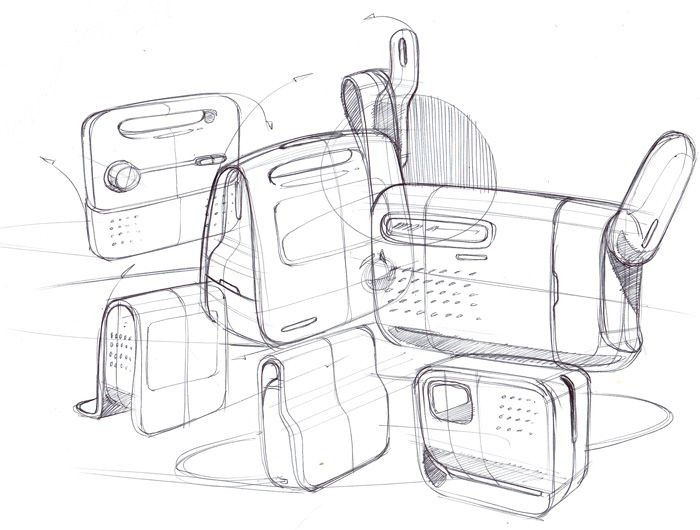
Design Evaluation
This stage can be called a prototyping stage. During this stage, designers should include additive manufacturing-specific design considerations into 3D models. 3D printing plays a major role in this stage as it allows designers to do rapid prototyping and validate the design. The design objective and identifying potential issues are the two important solutions provided by 3D printing. In-house 3D printing can keep the process moving and the creativity flowing by letting the product team create multiple prototypes. These prototypes can be built, tested, and verified in a shorter time period.
By providing 3D printed models to manufacturers and suppliers any miscommunications that can arise due to interpretation of CAD designs. Giving your manufacturers and suppliers an accurate representation of the end product could help prevent any miscommunication that could arise when interpreting the CAD models.
3D printing and prototyping can also help in design validation with the users. Choosing a set of beta users and allowing them to play with the prototype and helps product designers in understanding user behaviors.
I had a chance to introduce in-house 3D printing in Techolution/Faceopen to speed up our product design and development. We used PLA/ABS materials to do rapid prototyping of our custom devices. We couldn't achieve a 100% smooth outer finish as injection molding would provide but 3D printed parts helped us to validate the design and dimensions. Post-processing techniques like Sanding, Gluing, priming, and painting will result in a much smoother finish.

Planning Stage
Better planning allows the development team to take advantage of the resources available and to do capacity planning to distribute in-house and outsourcing. In this stage, the BOM should be finalized and teams should work on the best way to get the product on time to the market. Materials and manufacturing methods that are needed for the application (Ex: IP65 Rating, Compliance, and Certification needs) should be tested and chosen during this stage.
Manufacturing
At this stage, most of the small-scale and medium-scale companies tie-up with an established OEM to manufacture the product at scale. For lower volume, 3D printing offers freedom from traditional design and commercial constraints. For mid-high volume production, companies adopt CNC machining or injection molding.
コメント